Skanska’s UVA hospital expansion project, Virginia
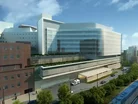
1. Could you provide an overview of your role within this new exciting project?
After becoming fortunate enough to win the project, I became part of the construction management (CM) team to help facilitate the design scope and cost as the constructor. University of Virginia Health System had the vision to procure designers and construction managers early in the Schematic Design phases. During the design phase, I led the Skanska team and participated with the designers to work on scheduling, cost estimating, cost trending, assembling Design-Assist subcontractors, value management, constructability analysis, construction phasing and document reviews.
I managed the procurement phase to secure a team of qualified subcontractors to work directly for Skanska. The construction phase services include construction administration and full responsibility for the successful completion of all construction.
2. What was the rationale for the expansion and renovation works?
UVA Hospital has seen significant growth in the number of patients visiting the Emergency Department. The emergency department, operating rooms and inpatient bed area comprise the expansion of the current emergency department. The new wing, including the emergency department, operating rooms and additional inpatient beds will provide 80 beds and enable the facility and its professionals to treat patients effectively, particularly those requiring special equipment.
The new wing of the department is being built on the site of the hospital’s ground helipad. It will include a six-story bed tower – three of which are shell space at this time – directly above the new wing, with a rooftop helipad. The first three floors are known as the Plinth, which will support the Emergency Department, along with dedicated space for mental health care, more operating rooms, expanded radiology services and cardiac labs.
The new construction is approximately 440,000 square feet and the associated renovation is approximately 90,000 square feet, through many phases. The work will encompass new drop off and entries into the emergency department for ambulance and ambulatory patients.
3. What stage is the project at currently?
The project is summarized in 4 major phases:
- The enabling projects are completed.
- The Plinth is underway with steel and concrete going vertical.
- The tower
- The renovations.
Currently the team has completed all of the enabling phases which include:
- MRI relocations
- 35KV work, which is high voltage electrical underground duct banks and manholes
- Emergency power site work
- Utilities on Lee Street, one of the streets bordering the project; inclusive of electrical, storm, sanitary, steam connections to the new construction
- Utilities on Crispell Drive, another street bordering the project; inclusive of electrical, storm, sanitary, steam and chilled water to the new building
- Air intakes and an ambulance-ambulatory temporary entrance.
With the enabling projects phased out of the existing site footprint, the team has now concurrently started construction on the Plinth and tower. We are currently standing steel on levels G, 1, 2, 2M and 3 of the Plinth. The east stair concrete shear tower has been topped out to its full height, approximately 175 feet tall. Our two tower cranes are in place and are servicing our project, the whole time coordinating this work with the still-active Trauma helipad located adjacent to our construction site. Currently we have $60 million dollars work in place.
4. How is technology helping you undertake work more efficiently and to a high standard?
The technology tools that we are implementing at UVA Hospital improve our communications, productivity, efficiency, first cost, life cycle cost, constructability, productivity, schedule and quality, to name a few benefits. Specifically, we enable utilisation with field connectivity; we install temporary infrastructure to support on-site data stations, deploy software programs, allow for mobility in the field using electronic tools; and use many communication devices from the field to the office. They all allow us to notify our construction team in “real time” and ensure the construction documents are up to date. We have found it to be an essential part of our success in providing a quality project to our customers. Construction documents include plans, specifications, safety programs, modelling, submittals, tracking programs, inspections, clarifications, schedules and many other aspects.
5. What technologies are you using for this particular project?
For this project, we have elected to use various programs by Autodesk. We have found that their systems are user friendly for all members of the construction team as well as provide detailed information about the status of the project.
We are using the Revit, Navisworks and BIM 360 Glue programs for the coordination of the mechanical, electrical and plumbing (MEP) trades. These systems do well in detailing the required information in addition to presenting an overview of site logistics to owner representatives.
For quality control, we have implemented the use of BIM 360 Field which provides us with more than ample documentation of Owner, Designers and Contractor concerns and inspection items in the field, in addition to the most current construction documents. This tool has allowed Skanska to document everyday milestones and challenges that are encountered throughout the project.
There are many additional levels and layers of technology applications that are implemented for every CM employee. Through the use of high speed internet, multiple servers, Wi-Fi accounts, smart boards all as a home base in the collaborative, big room job trailer we are able to execute our technology plan daily. Our plan starts early in pre-construction and is then implemented daily in construction, which includes:
- Noise/vibration inSite Monitor
- Primavera P6|Oracle
- Virtual reality tools
- Mobile technology
- A SharePoint portal
- On site kiosks with real time information.
6. Is data an important part of Skanska’s operations?
“Real time” data is essential to the delivery of a quality project. At the peak of construction there will be approximately 400 workers who must be notified of changes that occur in design. The technology available allows our team to implement these changes in the field and provide the most current information.
7. Is sustainability an important part of Skanska’s project delivery?
Sustainability has become integral in the measurement of success for construction. Skanska is proud to utilise the most advanced technology to ensure our team delivers the most green construction available. The team is well versed in LEED projects and is committed to environmental, economic and social sustainability. This project is designed and being constructed to a LEED Silver project list following the LEED 2009 for Healthcare, USGBC document.
8. What are some of the technology challenges you have faced throughout the project?
A successful construction project requires a collaboration of individuals from various backgrounds. These backgrounds often stem from a mixture of traditional construction methods to new technologies that have not yet been tested in the field.
The biggest hurdle faced as a Construction Manager is maintaining patience with new users. To overcome these challenges, Skanska pushes construction team members to attend regular training sessions and have resources readily available on a national and international level.
It is a challenge to implement new technology to improve efficiency, yet margins are extremely competitive, projects are complex, access to a skilled labour force is tight and wage pressures are mounting.
Communication and updating as a team continuously with remote resources located around the country or internationally is another challenge. We also have to ensure that the temporary infrastructure is set up to handle the high-tech requirements to implement all the new technology and handle the volume of users on a large project.
We also must be able to hire, train and retain a skilled workforce on a project from start to finish that have the proper background to implement the technology. It is a hot market and the employees with this skillset are in high demand.
Finally, it is crucial to communicate and utilise the advanced and changing technology to all levels on the project. We have to ensure the most technical of engineers; the creative architects, finance people, superintendents, and the skilled worker in the field can all obtain useful and real time data all at the same time.
9. Are there any emerging technologies to watch out for in the construction industry?
With the ever-increasing volume of technology, Skanska is constantly looking for the best ways to improve quality and production. Lately we have seen the emergence of artificial intelligence and the utilisation of virtual reality. In upcoming years, we could see the use of artificial technology for interpretation of construction documents which would drastically improve the daily production for Project Managers.
The use of Virtual Reality will be a tool to convey the design for our customers. We envision that this tool will provide our customers with a clear design intent without the use of mock-ups, saving the client both time and money. This is already being utilised on this project to some degree.
Robotics and Mechanised construction aspects will be emerging as an option, due to the skilled trades people becoming harder to find when the market is hot. The ever-improving sustainable technologies such as wind, solar and water will also be constantly incorporated into projects as these industries improve and become more cost effective.
Follow @ConstructionGL
Read the April 2017 issue of Construction Global
- BIM: Revolutionising Construction Through Digital InnovationPlanning & Design
- Skanska & Holcim Lead way on Sustainable Roads ConstructionBuilt Environment
- LEED: Building a Greener Future for ConstructionSustainability & Green Building
- Focus on: Construction Projects Life Cycle & ChallengesPlanning & Design