Warm Mix Asphalts and its key role in cutting emissions
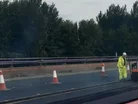
Highways England is urging all those involved in the construction and maintenance of the strategic road network, particularly designers and main contractors, to use warm mix asphalts (WMAs) as it moves towards net zero.
WMA technologies can offer enhanced efficiencies and lower production carbon, with CO2 savings of up to 15% when compared to conventional hot mix asphalts.
While typical asphalts are produced at up to 190°C, the simple principle behind WMA technologies is to manufacture asphalt at reduced temperatures but with additional additives, thereby using less energy and delivering meaningful carbon savings, without compromising performance. The most common techniques are organic additives, chemical additives and foaming techniques.
Produced at temperatures up to 40°C lower than traditional asphalt, if all production in the UK switched to WMAs, it would save around 61,000 tonnes of CO2 a year, the equivalent of cutting around 300 million miles of car journeys. It would also help save up to £70 million a year through an increase in shift outputs and it can be recycled back into new asphalts, preventing waste.
Another element is water consumption. WMA technologies operate above 100 degrees, so the amount of water remaining in the mix is very small. Various techniques are used to reduce the effective viscosity of the binder, enabling full coating and subsequent compactability at lower temperatures.
After a slowdown in 2021, the Asphalt additives market is likely to regain its growth momentum from 2022, ultimately reaching an estimated US$3.7 billion in 2026, according to ResearchAndMarkets.com.
Malcolm Dare, Executive Director of Commercial and Procurement at Highways England, said WMA marks a big step forward for Highways England that allows it to not only achieve huge efficiency savings but also reduce carbon as it strives for net zero.
"Carbon reduction, along with ensuring our roads provide smooth, safe, and efficient journeys for motorists, are key and something we are constantly striving to improve for generations to come," he said. "That’s why we are altering our way of working to encourage and enable the use of warm mix asphalts as standard across the supply chain."
WMAs can be laid using existing equipment and brings other benefits, including:
Carbon reduction
The lower production temperatures of WMAs reduce the carbon emissions associated with asphalt production by up to 15% compared to Hot Mix Asphalts. More widespread use of WMAs will help Highways England to achieve its aim of net zero by 2050.
Increased productivity
Reduced laying temperatures mean that WMAs take a shorter time to cool so greater volumes of asphalt can be laid in one shift, or the finished surface opened earlier to traffic without the risk of the material deforming under heavy loads. This will increase productivity by enabling more material to be laid within a working window, reducing the overall timeframe of the works and potential delays to motorists.
Improved health and safety
Reduced temperatures also help to reduce the health and safety risks associated with both production and laying of asphalt at high temperatures such as burns, exposure to fumes and the impact of steam on visibility, particularly when wearing safety eyewear. With WMAs, fume generation is reduced by around 50% for each 10°C reduction in temperature.
Improved durability
Due to being laid at lower temperatures and the increased amount that can be laid in a single shift, it also means less construction joints in the road requiring less maintenance in the future. This again increases the long-term benefits of the technology, life-time cost and need to undertake further maintenance.
Equivalent performance of WMA
Many studies show that the performance and the in-service characteristics of WMA mixes are equivalent to those of the traditional mixes, and frequently even better. The EAPA Position Paper The use of Warm Mix Asphalt gives a list of literature references of relevant studies.
It highlights two key benefits: alongside the energy reduction and lower GHG emissions, the significant lower bitumen fume exposure level during paving operations, compared to Hot Mix Asphalt, benefits workers.
"There are several reasons for the good performance of WMA," it notes. "As a result of improved workability, a higher compacted density can be achieved. This higher density reduces the long-term in-service hardening of the bitumen and also prevents ingress of water. Lower production temperatures can also decrease the ageing of the bitumen during the production stage which can additionally improve the thermal and fatigue cracking resistance of the asphalt."
- London Pioneers Sustainable Urban Heating InitiativeSustainability & Green Building
- Skanska & Holcim Lead way on Sustainable Roads ConstructionBuilt Environment
- Gensler Leveraging Climate Tech for Built EnvironmentSustainability & Green Building
- Barratt & Lloyds Combine to Kick-Start UK New Homes DriveConstruction Projects