Reinventing materials procurement in construction
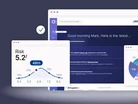
The question on how best to improve construction procurement looks a chicken-and-egg scenario: does the solution lie in technology driving sustainability or vice versa? Either way, the twin imperatives of sustainability and digital transformation cannot be ignored.
Agora recently announced its $33 million Series B funding round led by Tiger Global, with additional key investments from 8VC, Tishman Speyer, Jerry Yang, Michael Ovitz, DST, LeFrak, and Kevin Hartz.
To make our cities more affordable, the commercial construction industry must adopt new technology. Construction is a $10 trillion industry that employs more than 200 million people worldwide. Yet, according to McKinsey, labor productivity growth in the industry has been stagnant since 1947.
"Our cities are facing an affordability crisis," said Maria Rioumine, CEO and Co-Founder at Agora. "Our mission at Agora is to make the built environment faster and more efficient to build. By modernising the construction supply chain, we can dramatically reduce building costs and help make our cities more affordable and accessible to all."
Commercial trade contractors across the US still rely on manual, pen-and-paper processes too often to manage their supply chains. Office teams are overburdened with manual data entry and have to rely on outdated systems that don't work with each other.
Field teams have no easy way to select the exact materials they need and track them to delivery. These inefficient processes slow contractors down and lead to miscommunication, project delays, and a huge amount of waste.
Agora brings both field and office teams onto one digital platform that saves office teams 75% of the time they spend processing purchase orders, and field teams 38% of the time their foremen spend on materials management. In total, this amounts to $300,000 of potential annual savings for the average Agora customer.
Today, Agora is processing more than $140 million in annualised materials orders for its customers. In the last year, the company has grown revenue 760% and expanded across 30 states, all whilst tripling in team size. This strong growth attracted a number of top investors, who proactively offered term sheets and sought to scale Agora's impact.
"Agora is defining the future of procurement in construction," said John Curtius, partner at Tiger Global. "Agora's platform delivers an industry-leading experience for commercial trade contractors and is a game changer in modernizing how construction works. We're excited about Agora's strong traction, incredible market opportunity, and proven track record of customer success."
During the COVID-19 pandemic, contractors across the country faced severe supply chain disruptions and material price fluctuations. Many turned to Agora to help them manage quotes across different vendors more easily and lock in prices in advance. Using the Agora platform, customers reduced the back-and-forth ordering process that traditionally took five or more days to 24-48 hours, and saved their teams hours a day by eliminating manual data entry and shortening the time it takes to process each PO.
John Mraz, owner of Einheit Electric Construction Co, said Agora transformed the way it manages its supply chain. "With Agora, my foremen and purchasing agents can use a platform with Amazon-like speed and integration to make sure the right materials arrive on-site, on time. The digital experience is a boon for recruiting young workers, making the best use of our existing employees, and positioning the entire company to beat our goals and growth metrics."
Agora's latest round will boost its focus on recruiting top talent for its growing engineering, sales, customer success, marketing, product, and design teams. The company is also devoting significant resources to research and development as it expands into other trade verticals.
The construction sector has always faced criticism for its carbon emissions. Starting from the infrastructure to the particulate emissions left behind in the air, it acts as a source of air and sound pollution; this has pushed the sector toward finding more sustainable ways of building.
Governments across the globe are taking various measures to address the issue of pollution caused by the construction sector, said Roshni Nair, Lead Analyst at Beroe.
"Concepts like LEED certification have been implemented in most developed countries to ensure energy efficiency and reduce greenhouse gas emissions," she said. "However, several construction firms believe that sustainable raw materials to be a lasting solution to present issues. There are several innovative products in the market and under research that are environment friendly and help improve overall sustainability levels in a building."
Sustainable materials and green technologies have been implemented successfully in various sectors such as commercial, retail, industrial, and healthcare. Several construction firms in the US, Europe, and Asia have been actively using such green materials to reduce emissions and increase energy efficiency and overall cost savings.
The types of sustainable building materials include reclaimed wood, insulated concrete forms, bamboo, green thermal insulation (such as wool, polyester, hempcrete, and cellulose), reclaimed steel, bio walls, structural insulated panels, aerocon blocks, electrochromic glass, and recycled rubber.
The implementation of green building materials in construction will result in decreased operating costs of all facilities. Buildings with LEED certifications have recorded a 20 percent decrease in annual maintenance costs. They also tend to attract higher rents.
For example, in Los Angeles, a traditional building gets an average of $2.16 per sq. ft, but a LEED-certified one rents out for $2.91 per sq. ft on an average. The government has also implemented rules that improve energy efficiency in all buildings. With anticipated cost savings with these materials, this acts as a major driver of the green building material sector.
"The increasing need and growing demand for sustainable buildings worldwide mandate a change in traditional technologies and practices. This change can be brought about by adopting green materials in building construction, which will lead to better energy efficiency and waste management," added Nair.
"This concept has been successful in developed nations, and if replicated in other countries, it will help build long-term sustainable construction industry. In both developing and developed markets, the introduction of this concept along with advanced technology will improve the utilisation of available resources, construction products, and environmental conditions."
- Jacobs was recently selected to carry out essential engineering modifications as part of a $1.2 billion (ZAR 20 billion) program to extend the operating life of the Koeberg Nuclear Power Plant near Cape Town, South Africa. Koeberg is South Africa's sole nuclear power plant and generates 5% of the country's electricity. The project is in preparation for the installation of six replacement steam generators, each weighing about 380 tons and about 20 meters long, at the two-reactor plant operated by Eskom.