Beyond BIM: What’s next for the industry?
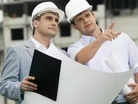
Gardens by the Bay (Singapore), Dongdaemum Design Plaza (Seoul, South Korea), Design Olympic Stadium: Bird’s Nest (Beijing, China), Ngurah Rai International Airport (Bali, Indonesia). What do these mega-structures in Asia have in common? They were all constructed using Building Information Modeling (BIM) solutions which have contributed to their landmark status.
With a boom in infrastructure projects expected in Asia – reported to represent approximately 60 percent of global infrastructure spending by 2025 – the industry has reason to continue feeling optimistic about the future. More emerging markets in Asia are aware that BIM is critical in achieving this ambitious targets too – as of 2014, the Construction Industry Development Board in Malaysia had invested an estimated RM1.5 million (USD340,000) on BIM awareness programs.
In Singapore, the BIM adoption rate is as high as 65% and the site productivity increased to 2 percent per annum for the last two years. It’s hard to deny the benefits of BIM – increased visualization allowing for better resource allocation and greater accuracy when planning for future rework, which ultimately yield increased efficiency. With the utilization of BIM technology fast becoming the industry standard, it is well worth looking into other future construction trends, and tapping on to them in 2017. From new construction techniques to project management solutions, they are forces to be reckoned with – sooner rather than later.
1. Design for Manufacturing and Assembly (DfMA)
With massive urbanization comes a greater need for more sustainable BIM data management and construction. In addition to BIM offering better ways of working, DfMA makes data exchange at the earliest stages of a project, a priority. This allows for error-free communication and streamlines collaboration throughout the construction lifecycle.
The implementation of DfMA simplifies the planning phase by transforming the traditional, siloed industry into one that encourages effective business collaboration. By integrating processes covering the entire construction workflow – from structural design to manufacturing to site – BIM system would empower architects, engineers, general contractors, subcontractors and suppliers to make decisions anytime, anywhere.
In the UK, the adoption of DfMA has been identified as a game changer in achieving the UK Government’s Construction 2025 blueprint which spells out targets for the construction industry – 50 percent faster delivery and 50 percent lower greenhouse gas emissions – in the next decade.
2. Prefabricated and prefinished volumetric construction (PPVC)
Remember the fun of playing with Lego blocks? Well, PPVC uses a Lego-like assembly method to build structures in a modular fashion. Depending on the complexity of projects, PPVC processes have the potential to improve onsite productivity by up to 50 percent thereby reducing the amount of labour required on-site by as much as 25 – 40 percent.
The speeding up of construction not only brings cost benefits but also a more sustainable and environmentally friendly future. As more activities are done off-site, a reduction of environment pollution and an improvement of site safety can be ensured. From residential developments such as The Wisteria in Singapore to mixed-used integrated building, the usage of PPVC is gaining traction.
Industry regulators are also beginning to recognize that efficient technologies such as PPVC is revolutionizing the way we build. In Singapore, Government Land Sales project regulations stipulate that at least 65 percent of the total constructed floor area of the building must employ PPVC. This regulatory requirement offers flexibility and systemization of PPVC design for buildings under construction and even provides maintenance guidelines for existing buildings.
3. Virtual Design and Construction (VDC)
With construction and demolition waste in the UK amounting to as much as 100.23 million tonnes a year – largely due to fragmentation and lack of interoperability between tools to share information between project participants – the construction industry needs to adopt a more integrated approach between multi-disciplinary stakeholders.
As its name suggests, VDC integrates various phases of a project and allows all stakeholders to collaborate virtually. Often a part of a mixed reality solution suite for construction site safety planning, inspection, and analysis, VDC essentially improves collaboration, project transparency, leading to time and cost savings.
It is also said to have the potential to transform work processes to the extent of improving productivity by over 20 percent compared with conventional methods of construction. In effect, it enables you to rehearse in a virtual environment before the actual physical construction starts!
Next generation BIM shapes construction’s digital future
PPVC, DfMA and VDC are exactly the kind of new technologies that the industry is looking for and are available without huge investment. However, it should be noted that leveraging BIM technology across the value chain is still integral to reap the full potential of the above-mentioned technologies. For example, an integrated BIM-VDC or BIM-DfMA approach will support a truly digital model to drive production planning and automation.
The introduction of such lean construction thinking streamlines work processes and makes way for further digital collaboration and innovation. Digitizing project management workflows has substantial benefits. Its greater use in the construction-planning process and on the construction site itself will enable firms to gain insight into advanced analytics of construction projects which can help to improve efficiency, timelines, and risk management.
Today, regulators such as the Building and Construction Authority in Singapore and the Construction Industry Development Board in Malaysia already playing an important role in defining new standards for emerging technologies (at least in public projects). Now the onus lies with the industry to develop digital roadmaps and train the next generation of building and construction experts to be adept at these digital technologies and solutions.