Cemex’s roadmap to decarbonising the cement industry
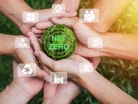
Annually, the global construction industry produces over 4.4 billion tonnes of concrete to build the roads, bridges, and buildings we rely on to live in and travel on. Its versatility makes concrete the most-used manufactured material in the world—with usage quadrupling from 1995 to 2022—but also one of the most polluting.
A large fraction of the CO2 emissions attributed to concrete production is a result of the production of clinker, a key component in cement, one of the core elements used to manufacture concrete. Clinker is traditionally made by firing fossil fuel-powered kilns filled with limestone and clay to high temperatures, where carbon emissions are released at two different stages during clinker production: first when burning fossil fuels to fire the kilns, and second from the chemical reaction triggered when limestone is heated and decarbonated. Together, these industrial processes contribute to 8% of the world's greenhouse gas emissions.
In attempts to combat concrete’s harmful environmental impact, the Global Cement and Concrete Association (GCCA) recently called on companies to end coal-generated electricity in cement production. Instead, the association urges them to work with governments to speed up decarbonisation and meet the UN’s carbon emissions targets.
Subsequently, world leaders in cement production, like Cemex, have committed to ambitious climate objectives and numerous decarbonisation efforts, and every concrete manufacturer worldwide must follow suit. Here’s Cemex’s roadmap for success.
Set clear goals
In 2021, Cemex set a target of below 475 kg of CO2 for 2030, representing above 40% reduction in emissions, under its Future In Action program focused on sustainable excellence through climate action, circularity, and natural resource management. It became one of the first companies in the global cement industry to validate its 2030 carbon reduction goals through the Science Based Targets initiative (SBTi), for alignment under its 1.5°C scenario.
The company’s other 2030 goals include increasing alternative fuel usage to 35%, achieving 41% less carbon content in concrete, and reducing transportation emissions by 30%, among others, in order to reach its ultimate goal of becoming a net-zero CO2 company in 2050.
Collaborate with sustainably focused companies
Cemex's ambitious program concentrates on six pillars, one of which is Innovation & Partnerships. In that regard, Cemex acknowledges that in order to achieve its goals it must collaborate with innovation-focused companies to implement new technologies and solutions across its multiple operations worldwide. Here’s how:
Goal 1: Boost clean energy consumption by 35%
To comply with its goal of increasing alternative fuel usage to 35%, it invested in HiiROC, a world-leading technology company that uses thermal plasma electrolysis to generate low-cost, zero-emission hydrogen. Hydrogen in cement production can be used in lieu of fossil fuels, significantly reducing CO2 emissions since the by-products of burning hydrogen are water vapour and carbon black. HiiROC’s low-cost hydrogen solution permits Cemex to substitute its use of finite raw materials such as natural gas and coal and scale the use of clean energy across its operations.
Since approximately 40% of the cement industry’s CO2 emissions come from firing kilns, Cemex has also partnered with solar energy startup, Synhelion. The cement manufacturer installed Synhelion’s solar receiver at its IMDEA Energy solar tower in Madrid. The pilot delivered record-breaking temperatures beyond 1500°C by heating a gaseous heat transfer fluid, generating the necessary process heat for clinker production. The use of hydrogen and solar energy are just two examples among many others of Cemex’s commitment to cleaner energy consumption.
Goal 2: Reduce CO2 in concrete by 25%
Cemex has teamed up with Carbon Upcycling to improve its Carbon Capture and Utilisation (CCU) efforts. The cleantech startup helps reduce CO2 in two ways, by recycling industrial waste that would otherwise end up in landfills and by using captured carbon to produce a low-CO2 concrete. Together with Carbon Upcycling, Cemex aims to double its industrial residue use to 6 million tons annually by 2030, significantly reducing its carbon footprint.
In addition, the leading cement manufacturer has internally developed Vertua, a low-carbon concrete. Vertua is essential in transitioning the built environment to net zero without compromising performance. Vertua has a CO2 reduction of at least 25% versus traditional cement, and in concrete, the CO2 reduction ranges from 30% to a full net-zero option.
Goal 3: Become net-zero by 2050
Cemex is working on a localised scale at selected cement plants to capture CO2 effectively and cost-efficiently, with the intention to later scale these technologies to become fully net-zero by 2050.
On that front, Cemex joined in 2022 Chevron, Saudi Aramco, Samsung Ventures, and AXA in funding Carbon Clean, a Carbon Capture startup, for a second time, bringing the total capital raised in this Series C investment round to $150 million. Furthermore, Cemex’s partnership with ETFuels, an off-grid green fuel production company, will support circularity in the CO2 lifecycle. Cemex will provide up to 450,000 metric tons of captured CO2 annually for ETFuels to produce electro fuels for use in the transportation industry.
Encourage investor and governmental action
Due to the high cost of decarbonisation technologies, the private sector must look to alternative sources of funding for financial support. To gather capital for industry-scale projects, Cemex is setting an example and has received numerous grants from public bodies such as the European Union (EU), the U.S. Department of Energy (DOE), and the UK Research Institute (UKRI).
Cemex’s current portfolio of decarbonisation projects has the potential to avoid more than 3 million tons of carbon emissions a year. These projects include:
- A €4.4m grant from the European Union for implementing WtEnergy’s waste-to-fuel technology using synthetic gas at Cemex’s Alicante cement plant in Spain.
- A US Department of Energy-funded FEED study, in collaboration with the independent nonprofit research institute RTI International and SLB, to develop a large-scale CCS at Cemex’s Balcones Cement Plant in Texas.
- A $3.2m grant from the U.S. Department of Energy for a joint project headed by Cemex, Sandia National Laboratories, and Synhelion, which aims to decarbonise cement projection with solar energy.
- £2.3m in funding from UK Research and Innovation (UKRI) to Carbon Upcycling for a consortium including Cemex to develop the world’s first commercial-scale cement additive plant that combines CO2 sequestration and waste glass.
Concrete structures are the bedrock of our built environment, and with the demand for construction services at an all-time high, concrete manufacturers, startups, researchers, and governments must work together to create a net zero carbon footprint and drive sustainable construction.