Off-site Building Benefits From External Forces
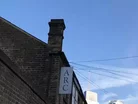
One of the COVID-19 corporate catchphrases must be ‘the acceleration of existing trends’ and it’s particularly apt when you look at the remote construction sector. While the world made harsh adjustments to remote working, for modular companies it was business as usual as rivals struggled to maintain schedules and reduce costs.
When you add to the mix ongoing COVID disruption, renewed focus on sustainability and net zero targets, constant pressures for new housing and ongoing digital transformation, it’s hardly surprising modular is experiencing new momentum.
Working on site is clearly no longer the only modus operandi and off-site’s appeal is its versatility across residential, commercial, education and healthcare sectors – the latter, in particular, has seen a spike in demand for hospital and quarantine-related prefabricated projects.
But it is housing which is the primary driver. With England alone needing 345,000 homes to keep up with demand, modular is looking an increasingly key element of the development puzzle.
The term ‘Modern Methods of Construction’ (MMC) has been banded around the industry for some time but it has only been in the last six to seven years that stakeholders have begun to embrace them. As part of new building regulations, all new-build homes constructed from next year onwards will be expected to produce 31 percent lower carbon emissions.
More developers are turning to modular as it lies in a sweet spot in the construction, environment and technology triangle.
Stewart Milne Timber Systems (SMTS) recently selected IFS to optimise offsite manufacturing, enabling it to expand into areas of new automation and robotic technology. IFS Cloud ERP will help it increase efficiency, maintain quality and reduce lead times and processing time associated with manufacturing and installing offsite systems and enable the company to work “smarter, quicker and greener,” according to Craig Thornhill, Finance Director at SMTS.
Social housing provider Stonewater and Boutique Modern, the UK’s first certified B Corp modular construction company which aims to be carbon neutral by 2025, have sealed a deal for 40 energy efficient modular homes to be delivered in Peacehaven, East Sussex.
The short distance between the construction factory and the development site means that the entire project, from the build process through to the transportation of the completed homes, will be as carbon efficient as possible. As part of its quality assurance, Boutique Modern undertakes frequent ‘health checks’ on the materials used; the company is working towards removing all inherent plastics in the insulation and other materials used to construct its homes, and no single-use plastic will be used to develop Stonewater’s modular home scheme.
Elsewhere Herefordshire Council has approved plans for a development that will see the delivery of 120 factory-built affordable homes – one of the largest of its kind in the UK. The scheme is being delivered through a £23 million partnership between modular housing company ilke Homes and Stonewater. All homes will achieve at least a ‘B’ Energy Performance Certificate rating, making them more energy-efficient than 92 percent of the UK’s housing stock.
With better thermal efficiency and massively reduced waste, factory-built houses are being seen as the only way that councils and housing associations can meet tougher building regulations and incoming targets on reducing carbon emissions.
“As well as dealing with the growing construction skills crisis, many are turning to modular housing due to the speed,” writes Stephen Stone in a blog.
“Foundations and utilities can be completed while homes are manufactured in factories, meaning it’s possible to complete a development in one third of the time compared with traditional construction methods. This is attractive to investors and housing associations who are making up a growing slice of the housing market, as it means they can generate income far quicker.”
Global movement
In the US, construction is underway at the Mission Rock development in San Francisco and prefabrication is playing a major part. The 28-acre mixed-use development, which has been estimated at $2.5 billion, is a public-private partnership between the Port of San Francisco, the San Francisco Giants and commercial real estate company Tishman Speyer.
Prefabricated building systems firm Clark Pacific worked with the owners and design firms, Henning Larsen, MVRDV, Studio Gang and WORKac to come up with a prefabrication solution that would also achieve the aesthetic of the project, which will feature natural and iconic California scenes on the exteriors.
Jim Lewis, director of sales at Clark Pacific, said the kind of early collaboration between the prefabrication and Mission Rock teams was similar to how the company worked on the Apple ‘spaceship’ headquarters in Cupertino, California, and is necessary to achieving a design-prefab balance.
APPLE PARK - The Spaceship - YouTube
Using prefab on such high-profile projects, Lewis said, should help debunk the misperception that prefab elements are always utilitarian. “It’s totally changing that,” he said. “You can do iconic architecture and do it prefabricated. You just have to start early … it’s a gamechanger.”
The steel prefabricated buildings market expects to observe an incremental growth of approximately $3 billion by 2026, according to ReportLinker.com. Steel reframes observe high adoption in prefabricated buildings due to lightweight, ductility, and recyclability, and these reframes are witnessing high acceptance in the construction sector as they can absorb wind turbulence and offer high elasticity during earthquakes.
However, with the outbreak of the COVID-19 pandemic in Europe, manufacturing activities and steel-using industrial sectors were shutdown, which affected steel demand. The EU28 steel consumption declined by -25.5% YOY in the second quarter of 2020 after witnessing a drop of -12% in the first quarter due to the onset of the pandemic.
Modular construction in European and US markets has the potential to deliver annual savings of up to $22 billion, according to McKinsey research. Countering the old reputation of prefabricated housing as an unattractive, cheap, poor-quality option, some builders are focused on sustainability, aesthetics, and the higher end of the market,” it reports. “New entrants and first movers that are unwilling to tolerate the industry’s fragmentation and lagging productivity are starting to disrupt the market and change the mind-sets of incumbents.”
Safety is also a significant factor. The Malaysia Department of Occupational Safety and Health (DOSH) has urged the construction industry to use drones or remote sensing devices to reduce risk of accidents at work. DOSH director-general Zailee Dollah said the use of both technologies is seen to be effective in ensuring compliance with occupational health and safety.
Off-site benefits
- Reduction in Waste materials
- Shorter build times
- Controlled build environment
- Made to order
- Less noise, dust and local disruption
- Fewer workers on site
- Creation of employment in areas away from the building site
- Transport from factory to site
- Cost
- Economies of scale
- Computing and traceability of components
Source: www.buildoffsite.com
Environmental benefits
- Industrialised modular construction leads to 50% less CO2 emitted per project
- If a building stops meeting and owner's needs, the elements get a 'second life' in a different arrangement or at a new location
- No less than 80% of the components in modular construction are reused. The approach creates value, as well as significant sustainability gains
Source: Jan Snel
- London Pioneers Sustainable Urban Heating InitiativeSustainability & Green Building
- Aggreko: Construction Working Towards Net Zero GoalsConstruction Projects
- Deloitte: Green Steel is Scope 3 Answer for ConstructionSustainability & Green Building
- CTP Embarks on Sustainable Pharmacy Hub in CzechConstruction Projects