Using robots to boost efficiency and drive faster fulfilment
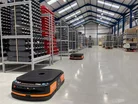
At one time, robots were seen as the future. But the future is now.
Robots are now being utilised to provide fast fulfilment for warehouses across the UK, providing fantastic solutions, rapidly moving materials and helping businesses achieve faster picking times than manual techniques.
With the ability to operate both day and night, businesses are achieving up to a 200% increase in pick rates and up to 300% increase in warehouse throughput. Robotics engineers over the years have been working hard to develop new robotics, artificial intelligence, and methods of effective automation. Typically, robotics work on the basis of machine learning and AI, Software for warehouse management, with sensors and response proficiency.
Warehouse Robotics
AMR’s – Autonomous Mobile Robots
Using sensor technology, AMR’s deliver inventory throughout your warehouse, with the capability of manoeuvring around the space without being guided by tracks and or a set route around the building. The key thing about Autonomous Mobile Robots, is their understanding of their environment which is enabled using sensors and software allowing for understanding of maps.
Using the process of maps, the robots have the ability to navigate around obstacles in their way, moving around the warehouse easily, minimising the need for human interference that could be considered time consuming and costly.
The idea behind these robots is to considerably reduce the amount of time warehouse workers spend on picking and sorting, therefore utilising manual resources elsewhere in the business. By today’s standards, these robots deliver accuracy, 24/7 around the clock. The level of accuracy provided means inventory levels are consistent and precise. This is done by regular stock counting each day, which makes a considerable difference when compared to counting stock just a few times per year. Businesses can now stay on top of their stock, keeping an eye on changes in numbers.
Automated Guided Vehicles (AGVs)
An Automated Guided Vehicle transports your inventory around your warehouse, using magnetic strips or tracks. Not all AGVs follow a track which means they have additional features for safety and guidance, including software that can map around your warehouse safely and seamlessly.
AGV Navigation
AGV’s are generally navigated by the following:
- Magnetic Tape
- Light Detection and Ranging – Sensors that transmit a laser pulse that measures the distance between objects and the AGV
- Vision Guidance – Cameras recording the route allowing the AGV to navigate
- Geo-Guidance – Similar to vision guidance only the AGV recognises objects around them allowing them to understand their location
- Laser Target Navigation
- Gyroscopic Navigation – Computer controlled AGV’s through transponders embedded into the warehouse flooring to determine that the AGV is taking the correct route
- Wired Navigation – Wire paths for the AGV to follow with a built-in sensor
The latest in warehouse automation
We’ve seen the Q3 robot in action and it is something very special! The Q3 is a great solution for ecommerce, 3PLC, and other warehouse circumstances, improving efficiency, reducing operational costs, and bringing a return on investment of around 12-24 months.
With dual-wheel differential drive, the Q3 provides an extremely smooth and seamless navigation of your inventory throughout your warehouse at a great speed, working with visual sensors and inertia providing an accurate journey throughout your warehouse.
That said, the Q3 robot can work safely alongside your manual workers utilising the laser technology, accompanied by ultrasonic and infrared obstacle avoidance. The flexibility of this AMR means there is no need for rails, tracking, or any fixed infrastructure that can hinder the performance of your warehouse.
Installing AMRs in warehouses today allows for:
- Robotic payloads
- Automatic charging zones
- 24-Hour warehouse operations
- Easily configured systems
The scalability, and customisation alone is highly beneficial to your throughput level, with the ability to scale up or down depending on your level of demand. Additionally, the volume of weight and products that can be transported at any given time, 24/7, around the clock is considerable.
Following the use of the Q3 robot in their warehouses, L&S Engineers have found an improved productivity rate of 40% and pick throughput up by 150%. Pick error rate has more than halved due to pick to light, touch screen, and static pick stations.
Replenishment throughput has doubled, and space utilisation is up by 26% with only 2 aisles being needed where 3 where needed previously. With a cleaner and tidier warehouse overall, stock has to be secured more carefully in order to avoid falling off the mobile racks, contributing to a more accurate level of stock.