Advanced tech and a fresh approach is helping construction firms 'go lean'
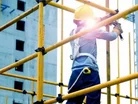
Challenges are forecasted for the construction industry in 2015, but they are different from the trials industry leaders faced in recent years. After a difficult start to 2014, the industry is recovering, adapting to new regulations and techniques, contending with labor and material shortages and implementing advanced technology. These factors create risk and potential setbacks, as well as tremendous opportunity for greater success in the new year.
The United States economy has continued to gain momentum, but the construction industry still dealt with the hangover from the downturn in 2014. The first six months of 2014 provided few new building opportunities. This was coupled with additional regulations, including healthcare reform and labor reporting, causing more hurdles for businesses. The sluggish market and time required to adapt to new guidelines bred an overall environment of cautious advancement. The turn came in mid-2014 as the market surged with a year’s worth of opportunities to be completed in just months. While the increase in work in 2014 was welcomed, those new regulations and requirements created unexpected extra costs that extend into 2015.
Those increased costs are just one issue that carries into this year as the industry works its way back from the recession. Companies continued to downsize last year, either through attrition or continued layoffs. The decrease in available workers could make it more difficult for companies to keep up with demand, which make joint ventures a likely path forward in the near-term. Companies will team up to handle the increasing demand, and owners may return to selecting a project team on a best value, rather than least expensive, basis.
While joint ventures allow for progress and probable industry growth, the labor-shortage problem is not going away. Even with a steady increase in demand, the industry probably won’t see a rise in labor. To begin to solve this dilemma, technical schools are working to revive and redesign their programs to attract a new generation of students to the construction field. In addition to improving education programs, passing comprehensive immigration reform will increase the labor pool and have an immediate, positive impact in construction. However, both of these measures will likely be a several year process, which means that the industry must rely on other measures, such as new building techniques and industry-wide collaboration, to continue its forward momentum.
Experimenting with new building techniques is always an evolving process, but it also provides a method to help address the labor shortage. Traditional practices involve bringing materials to the job site to erect a building. This takes time and is expensive compared to prefabrication techniques. Prefabrication is just what it sounds like: assembling a structure in a warehouse or other manufacturing site, transporting completed sections of structure to the site and putting those sections together to create the final structure. Long used in the housing industry, the practice is finding inroads in the commercial and industrial spaces as well. The approach allows businesses to take into account conditions of materials, natural elements, budget and labor, as well as providing a means of fixing issues more quickly than when building on site. Prefabrication techniques are advancing quickly due to technology improvements, which aid in reducing costs and completing builds with less labor.
Co-construction is another technique industry leaders are using to help combat labor shortages and limited resources. Co-construction is essentially allowing one team to build upon another’s work to collaboratively complete a project. While more companies are creating these teaming agreements, there is some risk involved. Co-construction leaves room for error and miscommunication. Effective co-construction incorporates sharing accountability in a fair and reasonable manner, while not creating an undue burden on the owner. Still, the practice has the potential to better serve and benefit owners as well as the teaming companies delivering the project.
Technology advancements help mitigate risks associated with co-construction as well as provide a platform for the industry’s early adopters to effectively progress in the coming year. Companies are implementing those technologies that allows for faster construction processes and more efficient use of the limited labor pool. Although some industry leaders are less comfortable with the ever-changing technology, the need for faster, more efficient techniques will likely outweigh, or at least lessen, any reluctance.
The construction industry is at an exciting turning point right now. We’ve collectively weathered the worst of the storm and see a bright path forward to create new industry standards for the coming year and beyond. In many ways, the downturn has forced the industry to reexamine its practices, technologies and overall approach to delivering projects. The opportunity for increased efficiency due to co-construction, prefabrication and advanced technology is great, but success will depend, in part, upon the open-mindedness of industry leaders and the incorporation of multigenerational ideas of how to improve the construction process.
- Mammoet installs first villas at Sheybarah Island ResortConstruction Projects
- Emerson to build state-of-the-art manufacturing hub at SPARKTechnology & AI
- InEight innovations focus on earned value management metricsTechnology & AI
- Adapting to new construction site-safety guidance with techConstruction Projects