Electric Construction Machinery Growth 'is Significant'
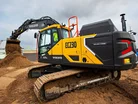
The global battery market for electric construction, agriculture and mining (CAM) machines is set to expand significantly.
Market research firm IDTechEx, which specialises in emerging technology analysis, has released data suggesting substantial growth potential in this sector.
The report reveals that construction equipment, particularly excavators, will be at the forefront of this transition. Large excavators, which typically weigh more than six tonnes, currently produce nearly half of all emissions from construction machines, making them a primary target for electrification efforts.
Construction professionals need to consider various factors when evaluating electric equipment options, with the report saying charging infrastructure installation on work sites remains a critical concern.
Data shows construction machine battery demands
The report also highlight that construction companies must assess whether electric machines can complete a full working day on one charge.
Battery requirements vary significantly between different types of CAM machines, the report states. It reveals that tractors use approximately 50% more energy per hour compared to other CAM equipment. This means they require larger battery capacity than vehicles such as mining light vehicles.
Current battery technologies used in CAM machines include lithium iron phosphate and nickel manganese cobalt, chemistries that have been adopted from the automotive sector. However, the report suggests new battery types may be better suited to construction applications.
Construction battery tech faces charging hurdles
The transition to electric machines presents several technical challenges. IDTechEx says CAM equipment requires faster charging capabilities than electric cars to minimise operational downtime. This creates a conflict between charging speed and energy density in current battery technologies.
Construction equipment manufacturers are exploring new battery chemistries to address these issues. The report says lithium titanate batteries could provide a solution, because they potentially offer more than 10,000 charging cycles before replacement. This compares favourably to the approximately 5,000 cycles available from current NMC and LFP technologies.
E-machines safety drives solid-state development
Safety considerations, meanwhile, are driving development of new battery technologies for construction equipment. The report's authors say solid-state batteries may provide enhanced safety features. This could prove crucial for machines operating in confined spaces, such as underground loaders or mini excavators.
Manufacturing challenges exist in producing solid-state batteries. IDTechEx explains that creating sufficiently thin electrolytes of adequate quality presents difficulties. Maintaining proper connections between electrolytes and electrodes also remains problematic.
Regional variations also exist in battery chemistry adoption. The report reveals that European and North American manufacturers predominantly use NMC batteries. Chinese manufacturers typically opt for LFP chemistry. Future technologies under consideration include silicon anode, solid-state, and sodium-ion batteries.
"The construction industry's transition to electric machines will require careful evaluation of multiple battery chemistries," says Dr Richard Collins, Technology Analyst at IDTechEx. "No single solution currently meets all the sector's requirements for power, longevity and safety."
- Caterpillar: Profile of a Construction Equipment GiantBuilt Environment
- Volvo CE: the Sustainable Construction Equipment SpecialistSustainability & Green Building
- Joint-venture battery factory in Vietnam breaks groundConstruction Projects
- Mercedes-Benz Arocs: Innovating constructionDigital Construction
Featured Articles
BCG report details how industries including construction need to collaborate on AI-driven energy solutions, citing data centre design as an example
Volvo Construction Equipment’s new Braås site is the first to earn the Climate Efficient Site certification, spearheading sustainability in construction
French multinational construction firm Bouygues Construction expands US presence as subsidiary Aimco lands luxurious Miami waterfront development
project