How Innovative Design Can Reduce Construction Costs
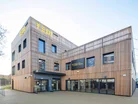
The construction industry is seeing unprecedented change, as new technologies reshape traditional approaches. This transformation is driving down costs while improving efficiency and sustainability. Innovation in construction design, for one, is revolutionising how buildings are conceived, planned, and executed.
The economics of construction have long been challenging, with projects frequently exceeding budgets and timelines.
Phil Bernstein, Associate Dean and Professor Adjunct at Yale School of Architecture says: "By leveraging digital design tools and prefabrication techniques, we can significantly reduce construction costs while improving quality and speed."
Digital design tools are leading this transformation, enabling precise planning and visualisation before breaking ground. Building Information Modelling (BIM) software creates detailed 3D representations of projects, identifying potential conflicts before they become costly on-site problems. Bernstein adds: "Advanced 3D modelling allows us to optimise designs and identify potential issues before breaking ground."
AI algorithms are now analysing thousands of design variations to identify optimal solutions.
Naji Atallah, Midmarket & Industry Director of Sales at Autodesk, says: "Generative design powered by AI is unlocking new possibilities in architectural and engineering design."
Atallah notes: "By rapidly exploring thousands of design options that meet specified criteria, we're able to identify optimal solutions that maximise performance while minimising material use and costs."
Autodesk driving digital transformation
Cloud-based collaboration platforms are transforming how design teams work together. Digital replicas are becoming essential tools for project optimisation. Donna DeMarco, Digital Delivery Specialist at Jacobs, says: "Digital twin technology is revolutionising how we approach building design and construction."
The integration of design and construction phases is reducing costly communication errors. DeMarco adds: "By creating virtual replicas, we can optimise designs, simulate performance, and identify potential issues before breaking ground. This proactive approach is helping our clients avoid costly rework and change orders."
Modular construction is reshaping traditional design processes, demanding new approaches to project planning.
Atul Khanzode, Chief Technology and Innovation Officer at DPR Construction, says: "Innovative design approaches like modular construction and prefabrication can significantly reduce on-site labour costs and project timelines."
Modular systems reshaping construction
Prefabrication facilities are becoming essential partners in the design process, says Khanzode, who notes: "By shifting more work to controlled factory environments, we're seeing 20-30% reductions in overall project costs on some of our large commercial builds."
Bernstein reveals: "Prefabricating building components off-site in controlled factory settings cuts on-site labour costs and minimises material waste."
Virtual Reality is emerging as a powerful tool for design visualisation and client communication. VR technology allows stakeholders to experience spaces before construction begins. This capability reduces expensive design changes during construction.
The technology enables more efficient design reviews and stakeholder approvals. Teams can conduct virtual walk-throughs to identify potential issues early. This approach is particularly valuable for complex institutional projects like hospitals and schools.
Virtual Reality is also transforming the training landscape for construction teams. Workers can now practice complex assembly procedures in safe, virtual environments. This preparation reduces costly mistakes and improves on-site efficiency.
Kingspan and sustainable material innovation
Sustainable materials are driving innovation in construction design, often with surprising economic benefits.
Kingspan, a global leader in high-performance insulation, is developing materials that improve both environmental performance and construction efficiency. Interface, a sustainable flooring manufacturer, produces modular products that reduce installation time and waste.
New materials are enabling more efficient construction methods while meeting environmental standards. Bio-based materials offer improved performance while reducing carbon footprints. These innovations are particularly important as environmental regulations become stricter.
The cost implications of sustainable design extend beyond initial construction. Enhanced energy efficiency and reduced maintenance requirements improve long-term economics. These benefits are increasingly important to clients focused on lifecycle costs.
Design innovation is fundamentally changing construction economics. The integration of digital tools, modular approaches, and sustainable materials is creating new opportunities.
Bernstein concludes: "Together, these innovative approaches can reduce overall project costs by 20-30% compared to traditional methods."
The future of construction design lies in the continued evolution of these innovative approaches. As technologies mature and new materials emerge, the industry will see further improvements in efficiency. The result will be more affordable, sustainable and higher-quality buildings.
Featured Articles
BCG report details how industries including construction need to collaborate on AI-driven energy solutions, citing data centre design as an example
Volvo Construction Equipment’s new Braås site is the first to earn the Climate Efficient Site certification, spearheading sustainability in construction
French multinational construction firm Bouygues Construction expands US presence as subsidiary Aimco lands luxurious Miami waterfront development
project