The Key to Modular Construction Success
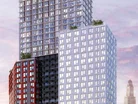
The shift towards industrialised design and construction such as modular construction, promises significant efficiency gains, cost savings and environmental benefits for the construction industry.
Modular construction can build most buildings, from offices, to healthcare facilities, to waste management centres and even bridges.
Construction giants like Skanska, the Swedish multinational construction and development company, are at the forefront of this revolution, with modular and prefabricated building techniques gaining momentum worldwide.
However, it's only in recent years that technological advancements and pressing needs for affordable housing have propelled the concept into the mainstream.
Today, Japan and Sweden are leading the charge. With Sweden having the highest proportion of homes being delivered using modern methods (around 45%) and Japan producing the highest number of new modular homes.
Bain & Company’s key to modular construction success
Modular construction has roots dating back to the 19th century, with prefabricated housing units used during the California Gold Rush.
Now, off-site modular construction offers compelling advantages over traditional building methods.
According to Bain & Company, the global consulting service, industrialised design and construction can reduce labour and material costs by up to 20%, decrease on-site labour requirements by 30% and slash construction timelines by 20% to 50%.
These efficiencies are particularly attractive for large-scale projects in rapidly developing regions like the Middle East.
Yet Brain & Company believe that despite its potential, modular construction still faces hurdles to widespread adoption.
The fragmented nature of the construction industry, with its myriad of stakeholders including investors, architects, manufacturers and builders, has slowed progress.
However, Bain & Company's analysis suggests that industry players will need to collaborate and share transitional costs to realise the long-term benefits of industrialised design and construction such as modular construction:
Construction companies
Construction companies are expanding into off-site assembly and manufacturing.
This shift requires improving digital design capabilities and reskilling the workforce in new assembly techniques.
As the boundary between builders and manufacturers blurs, scale will become more important, leading to industry consolidation.
Real estate developers
By focusing on long-term returns, real estate developers can navigate higher initial investments and set construction requirements that guide the design of standardised modules.
This approach promotes replicability and standardisation, incentivising designers and architects to adopt off-site construction methods.
Architects and designers
Architects and designers must enhance their digital design skills to create precise plans for modular components.
Close collaboration with manufacturers is essential to understand production possibilities and ensure designs are feasible for off-site manufacturing.
Manufacturers
Manufacturers have a unique opportunity to innovate and set new industry standards.
By focusing on strategic parts of the construction process and partnering with other module makers, they can capture a larger share of the profit pool.
Offering engineering support and installation guidance will further encourage the adoption of new standards.
How are construction leaders adopting modular construction?
Skanska has delivered thousands of modular homes across Sweden, Norway, Denmark and the UK.
The company has invested heavily in modular construction techniques, particularly in the Nordic countries where prefabrication is more established.
The company has also leveraged Building Information Modeling (BIM) and prefabrication techniques to deliver modular solutions.
BIM enables precise planning, coordination and visualisation, while prefabrication allows for controlled manufacturing environments.
Bouygues, a French construction company, delivers modular housing solutions across Europe for residential, student and temporary accommodation.
They utilise digital twins and VR simulations to optimise designs and enhance collaboration.
Meanwhile, Laing O'Rourke, a British firm, champions Design for Manufacture and Assembly principles, aiming for 70% off-site construction, 60% improved efficiency, and 30% faster project completion.
They've also implemented modular housing projects throughout the UK and Europe.
NELCO, a Dutch specialist in modular construction, focuses on residential and student housing.
They employ advanced manufacturing techniques, including robotics and automation, to improve quality control and production efficiency in their European projects.
******
Make sure you check out the latest news at Construction Digital, a BizClik brand
- Costain Doubles Profits: Legacy of Infrastructure InnovationProject Management
- Omya Boosts Construction Sector with Sustainable SolutionsSustainability & Green Building
- Top 10: Biggest Construction Companies in the USConstruction Projects
- How Insulation and Cladding Affects Modern ConstructionBuilt Environment
Featured Articles
BCG report details how industries including construction need to collaborate on AI-driven energy solutions, citing data centre design as an example
Volvo Construction Equipment’s new Braås site is the first to earn the Climate Efficient Site certification, spearheading sustainability in construction
French multinational construction firm Bouygues Construction expands US presence as subsidiary Aimco lands luxurious Miami waterfront development
project