Clean Energy Prompts Quest for new Cement Alternatives
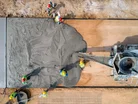
The move to clean energy is, ironically, jeopardising the main sources of low-carbon cement alternatives that are a by-product of burning fossil fuels.
Two products in particular will be affected: Fly ash -- a by-product of coal-fired power plants -- and ground granulated blast-furnace slag (GGBS), which is derived from coke-based steel manufacturing. These materials have been effective in reducing the carbon content of concrete, with GGBS in particular frequently used in major construction projects.
In recent years, the construction industry has turned to SCMs to decrease the amount of cement used in concrete. Cement production is responsible for a substantial amount of carbon emissions globally.
But the availability of these materials is expected to fall in the future, reports UK concrete industry body, the Concrete Centre, which provides best practice guidance, events and online resources to help the UK economy realise the potential of concrete.
Speaking to the Centre, Professor Leon Black of Leeds University explains: "With the decarbonisation of electricity -- and UK steel manufacture shifting to electric steel recycling furnaces -- SCMs will become increasingly scarce."
UK clay as an alternative to traditional SCMs
The Concrete Centre says that, to address the impending shortage, a team of researchers is investigating the potential of UK clays as alternative SCMs. The project, known as Eureka, is funded by the Engineering and Physical Sciences Research Council (EPSRC).
Professor Black is working alongside Professor Hong Wong from Imperial College London and Clive Mitchell from the British Geological Survey. Their goal is to determine the extent to which UK clays can be processed and used as SCMs.
The team is focusing on lower-grade clays as potential alternatives to metakaolin, an expensive SCM derived from china clay.
Prof Black stresses the importance of this research: "It might be usable as an SCM rather than simply for landscaping.
BGS maps clay distribution for Eureka Project
The BGS is playing a crucial role in mapping the distribution of suitable clays across the UK. It has already analysed approximately 60 clay samples from various locations, and says around a dozen samples "show promising characteristics".
To make clay suitable for use as an SCM, it needs to undergo a process called calcination. This involves heating the clay to around 800°C to make it reactive. While this process does have a carbon cost, it is significantly lower than that of traditional cement production.
Prof Black explains the environmental benefits of using calcined clay as an SCM: "You end up with an SCM with a carbon footprint roughly half that of Portland cement," he says. "This reduction in carbon emissions could have a substantial impact on the construction industry's overall environmental footprint."
Optimising clay processing for concrete industry
The Eureka project is not only focused on identifying suitable clay sources but also on optimizing their use in concrete production. After heating, the clay is milled into a fine powder. However, this can cause flow issues in concrete mixtures.
To address this challenge, the research team is collaborating with additives suppliers. They are working to develop solutions that will improve the performance of calcined clay in concrete mixtures. The goal is to maximize the amount of cement that can be replaced without compromising the concrete's quality.
Prof Black stresses the importance of practical application in their research. "We need to make it usable, and ensure newly developed materials satisfy industry requirements," he says. "The team is working with industry partners across the entire supply chain to achieve this goal."
Laboratory analysis has shown promising results for concrete containing calcined clays. The next step is to conduct practical testing to verify the performance of these materials in real-world conditions.
Prof Black concludes, "By the end of this year, we hope to have our first few tonnes of calcined clay ready for testing by industry."
- Global Coalition Targets Green Finance for Building SectorSustainability & Green Building
- Holcim & Neustark Partner on Construction Carbon CaptureSustainability & Green Building
- Skanska and Holcim Lead Low-Carbon Road Building RevolutionSustainability & Green Building
- Explainer: Formwork - Shaping the Future of ConstructionBuilt Environment