Skanska and Holcim Lead Low-Carbon Road Building Revolution
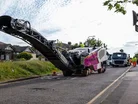
The road construction industry is undergoing a significant shift towards sustainability. Companies are developing innovative techniques to reduce carbon emissions in road building. These methods include recycling tarmac surfaces and using low-carbon cement.
Recycling tarmac surfaces involves removing the existing road surface and reprocessing it for reuse. This process reduces the need for new materials and cuts down on waste. The recycled tarmac is often mixed with new materials to ensure quality and performance.
Low-carbon cement is another key innovation in sustainable road construction. Traditional cement production is a major source of carbon emissions. Low-carbon alternatives use alternative raw materials or employ more efficient production processes.
Nick Harris, Chief Executive of the UK's Highways Agency, says: "We're committed to reducing the carbon footprint of our road network. Recycled materials and low-carbon cement are playing a crucial role in achieving this goal."
Other low-carbon materials are also being incorporated into road construction. These include recycled plastic, glass, and even waste materials from other industries. These materials can replace or supplement traditional road-building components.
The UK's Highways Agency is responsible for operating, maintaining, and improving England's motorways and major A roads. It plays a key role in implementing sustainable practices across the country's road network.
Skanska pioneers low-carbon techniques in M25 project
Swedish construction company Skanska has been at the forefront of low-carbon road building. A multinational construction and development company, Skanska is also known for its focus on sustainability and innovation in construction practices.
It has implemented several sustainable techniques in its projects across Europe, with a notable example being the recent widening of the M25 orbital motorway that skirts London. The M25 project involved widening sections of the motorway and upgrading junctions.
Skanska used a range of sustainable techniques, including recycling existing road materials on-site. including recycled aggregates, which reduced the need for transportation and lowered overall emissions. The company also used low-carbon concrete, reducing its carbon emissions by 40% compared to traditional methods.
A Skanska UK spokesperson said: "We also implemented a warm-mix asphalt technology. This allows us to produce and lay asphalt at lower temperatures, further reducing energy consumption and emissions."
Holcim develops ECOPact low-carbon concrete for roads
Swiss building materials company Holcim has developed a range of low-carbon concretes for road construction. Holcim is a global leader in building materials and solutions, operates in 70 countries. The company focuses on developing sustainable and innovative construction materials.
Its ECOPact product line offers concrete with up to 90% less carbon emissions than standard concrete. ECOPact concrete uses recycled materials and alternative binding agents to reduce its carbon footprint, and has been used in several road projects across Europe, including a major highway expansion in Germany.
Jan Jenisch, Chairman of Holcim Holcim, says: "The growing demand for ECOPact globally is a great demonstration of how we are part of building a greener world, from Argentina to the US. I congratulate our teams for making this happen and look forward to more successes ahead on the way to making Holcim the global leader in innovative and sustainable building solutions."
Low-carbon asphalt gains traction in Netherlands
In the Netherlands, major European construction company BAM has been pioneering the use of low-temperature asphalt. This technique, known as Low Energy Asphalt Concrete (LEAB), reduces energy consumption during production and laying. The company has implemented LEAB in several road projects in the Netherlands and Belgium.
The LEAB technique involves using special additives that allow the asphalt to be mixed and laid at lower temperatures. This not only reduces energy consumption but also extends the working life of the road surface.
Rémy van den Beemt, BAM Infra’s Head of Technology, says: "BAM is a forward-thinking company, which has always had its eye on the development of sustainable production methods. Our solutions enable us to contribute to the climate goals of our clients."
Van den Beemt adds: "We've used LEAB on over 100 projects in the past five years. The feedback from clients has been overwhelmingly positive, both in terms of performance and environmental impact."
- Global Coalition Targets Green Finance for Building SectorSustainability & Green Building
- Vattenfall Wind Farm Lays Foundations for SustainabilitySustainability & Green Building
- Cemex Names Most Innovative Construction StartupsTechnology & AI
- LEED: Building a Greener Future for ConstructionSustainability & Green Building
Featured Articles
BCG report details how industries including construction need to collaborate on AI-driven energy solutions, citing data centre design as an example
Volvo Construction Equipment’s new Braås site is the first to earn the Climate Efficient Site certification, spearheading sustainability in construction
French multinational construction firm Bouygues Construction expands US presence as subsidiary Aimco lands luxurious Miami waterfront development
project