‘Electric Cement’ Breakthrough Results in Zero CO2 Emissions
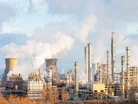
The world-first process, which has been dubbed ‘electric cement’, could shape the future of the construction industry.
Scientists from Cambridge University have succeeded in reactivating used cement by exposing it to high temperatures in cement kilns.
The Cambridge breakthrough saw scientists ‘piggyback’ on the heat generated by another heavy industry: steel recycling.
In steel recycling, chemicals are added that float on the surface of the molten metal, to prevent it reacting with the air and creating impurities, known as slag.
The scientists discovered that the composition of used cement is almost identical to the slag used in electric arc furnaces.
They are currently trialling the electric cement process in an electric arc furnace at the Materials Processing Institute in Middlesbrough.
Spanish company Celsa Group – a multinational group of steel companies – will now attempt to replicate the process at scale in its electric arc furnace in Cardiff.
The discovery, say the scientists, could not only drastically cut cement-related carbon emissions, but also make cement far cheaper to manufacture.
‘Electric Cement’ inspired from steel recycling
Commenting on LinkedIn, Google EMEA Sustainability Lead Adam Elman said he is “super excited” about the cement sustainability breakthrough.
“Cement is the modern world's most common construction material, but it is also a huge source of planet-warming gas emissions,” he added.
For leading global cement companies, including: LafargeHolcim, Anhui Conch, CNBM (China National Building Material), HeidelbergCement and Cemex, the world of cement could be about to change for the foreseeable future.
Lead Scientist, Cyrille Dunant, told the BBC that the innovation “could allow the production of zero-carbon cement”. He added that it would also make the steel recycling process less polluting, because manufacturing the chemicals used as slag also generates high carbon emissions.
Dunant says: “we have shown that the high temperatures in the furnace reactivate the old cement, and because electric arc furnaces can be powered by renewable power, the entire cement making process is decarbonised."
Other sustainable benefits from ‘Electric Cement’
As well as saving on CO2 emissions, the recycled cement initiative mitigates environmental impact by minimising waste in landfills.
Construction firms can use recycled cement for the construction of buildings, roads, and infrastructure projects, fostering a circular economy approach.
Meanwhile, collaborative efforts between construction and waste management companies, as well as regulatory bodies, could streamline recycling processes and help establish new sustainability standards.
It is hoped that government regulations and incentives will encourage recycled cement usage and drive widespread adoption.
All of which means it can help the construction industry meet its sustainability goals.
Researchers believe that if we switch to using electric-powered furnaces to make cement, and use renewable energy such as solar or wind instead of fossil fuels, there could be no greenhouse gas emission at all.
If cement was a country, it would be the third biggest source of emissions after China and the US.
Sustainable cement production breakthrough
The Cambridge research on ‘Electric Cement’, follows similar work on cement sustainability, undertaken by Christ Cheeseman, Professor of the Department of Civil and Environmental Engineering at Imperial College London.
Cheeseman aims to develop net zero cement technology via a CO2 capture process designed by ICL researchers.
The process transforms magnesium silicate materials like olivine, into cement materials, and will capture CO2 in a form that can be used in a variety of sustainable construction projects at the same time.
From breaking down olivine, silica can be used as a cement material added to concrete to make the mixture more economical, increase strength, reduce permeability, and influence other properties.
The new material should produce concrete that is also more desirable when it comes to strength and durability.
Regarding CO2, the remaining magnesia can be used to permanently isolate CO2, which results in magnesium carbonate, an extremely stable mineral for long-term carbon storage and no danger of leakage.
******
Make sure you check out the latest news at Construction Digital, a BizClik brand