Peri builds largest 3D-printed apartment building in Europe
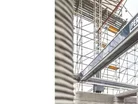
Work on the first 3D-printed apartment building in Germany is progressing and proves the technology is suitable for building large dwellings, according to German construction giant Peri.
Located in Wallenhausen, Bavaria, the project is the second 3D-printed residential building by the company – in September, the family-owned firm announced work had begun on Germany’s first printed residential house in Beckum, North Rhine-Westphalia.
Two months later, the company has launched work on a building that consists of five apartments across three floors, with approximately 380sqm of living space constructed, using a 3D construction printer. The residential building also features a full-length basement. The printing process for this project is expected to take six weeks, the company says.
“With the project in Wallenhausen, we are seeing the PERI 3D construction printing team take the next important step. At the same time, PERI is consolidating its position as a leading company in the field of 3D construction printing,” said Thomas Imbacher, Managing Director Marketing & Innovation at PERI Group.
“By printing the first apartment building in Germany, we are demonstrating that this new construction technology can also be used to print large-scale dwelling units. In terms of 3D construction printing, we are opening up additional areas of application on an entirely new level.”
The client is Michael Rupp Bauunternehmung GmbH, which will specialise in the 3D sector from 2021 onwards through its newly founded subsidiary Rupp Gebäudedruck.
“Our family-owned company has enjoyed 25 years of success in the industry and has an array of satisfied customers in the region. This means that we have the edge in terms of knowledge and can draw on a wealth of experience as we enter the 3D construction printing market,” said Fabian Rupp, managing director of Rupp Gebäudedruck.
His brother Sebastian, also a managing director at the family-owned company, adds: “At the same time, we believe that this new technology has enormous potential for the future, and we want to help shape that future. Despite the traditional nature of our craft, we are also innovative and do not shy away from new challenges – quite the opposite in fact.”
The planning architect is the architectural firm Mühlich, Fink & Partner BDA from Ulm. The materials used to produce the printable concrete are being sourced from HeidelbergCement. The mixing technology used has been sourced from m-tec mathis technik gmbh.
The engineering office Schießl Gehlen Sodeikat assisted with the preparation work for the warrant. The Technical University of Munich planned and carried out the relevant approval tests.
Once construction is complete, the apartments will be rented out to the public, although one of the apartments will be used as a show apartment.
PERI states that it is using the gantry printer BOD2 for this construction printing project. The system has a print head that moves about three axes on a securely installed metallic frame. The printer can move along its frame to any position within the construction and only needs to be calibrated once, saving time and costs.
During the printing process, the printer takes into account the pipes and connections for utilities that are to be laid at a later time. The BOD2 has been certified in such a way that it is possible to carry out work within the printing area while printing is in progress, Peri explains.
This means that manual work, such as the installation of empty pipes and connections, can be easily integrated into the printing process, it adds.
The i.tech 3D material that is being used to print the building in Wallenhausen was developed by HeidelbergCement specifically for 3D printing, the statement continues.
“The properties of i.tech3D are tailored to the specific requirements of 3D construction printing using concrete,” says Dr. Jennifer Scheydt, Head of Engineering & Innovation at HeidelbergCement. “Our material has excellent pumping and extruding characteristics and works perfectly with the BOD2 printer.”
Two operators are required to run the printer, and the print head and print results are monitored by a camera. With a speed of 1 m/s, the BOD2 is currently the fastest 3D construction printer available, taking around five minutes to complete 1sqm of a double-skin wall.