Top six benefits of offsite construction
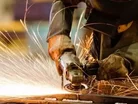
Offsite construction is a growing trend, with many companies growing wise to the advantages of moving the building process away from the physical site and into a controlled factory environment. Here, we take a look at some of the reasons why offsite is the next big thing.
Efficiency and predictability
By building offsite, the process is the same every time, meaning that each time the process is performed, the time taken can decrease. Work can be guaranteed to be delivered on time and to the highest quality, as the mitigating circumstances such as bad weather do not delay the project.
Safety
The factory is a far more predictable setting than the physical construction site, which eliminates the variables of weather and visibility. Having the conditions be the same every time makes errors much less likely. Most of onsite construction’s most dangerous hazards: like fall from height and equipment accidents, are not an issue in the factory.
Sustainability
Offsite construction requires less heavy machinery and less energy. Transporting the finished product to the site also uses minimal vehicles, and wastage is minimised, as material requirements can be more accurately calculated, allowing the company to make savings by buying in bulk.
Less labour
Studies have shown that far less labour is required to construct a building in a factory setting. The Steel Construction Institute (SCI) has claimed that hands required could be reduced by as much as75 percent on a four-storey residential development, savings that are similarly large in other kinds of build. Less workers of course means less wage costs for the company.
Less training
While training to be an expert in onsite construction is a lengthy process, teaching workers to perform their role is an offsite build is much simpler and faster. Transferring the construction process to a factory setting essentially turns building into a manufacturing process, and each worker need only learn their own small role in the production line. Less training means faster delivery and money saved.
No disruption to residents
An onsite build can severely test the patience of those unfortunate enough to live in the vicinity. Apart from the noise and air pollution of heavy machinery and equipment, construction and delivery vehicles travelling to and from the site can cause traffic delays and block parking spaces and access routes. This is a particular problem in constrained urban areas. Furthermore, construction works and cranes never look pretty and can be an eyesore for a long time. Moving construction away from the site and into a factory will be a great relief to local residents.
Featured Articles
BCG report details how industries including construction need to collaborate on AI-driven energy solutions, citing data centre design as an example
Volvo Construction Equipment’s new Braås site is the first to earn the Climate Efficient Site certification, spearheading sustainability in construction
French multinational construction firm Bouygues Construction expands US presence as subsidiary Aimco lands luxurious Miami waterfront development
project