Wincanton: How Infrastructure Downtime Affects Construction
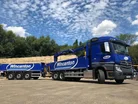
In the volatile state of global infrastructure development, a single hiccup in the supply chain can trigger a domino effect of delays, sending shockwaves through an entire project.
Wincanton, a leader in supply chain solutions and construction logistics management, has pulled back the curtain on this critical issue, offering insights into downtime in the construction industry.
Small and medium-sized enterprises often bear the brunt of delays, The Wincanton report delves into what's at stake when delays hit, and and details how interruptions can derail a project's success?
In infrastructure projects, downtime can strain budgets, regardless of scale. Delays in material delivery or equipment availability disrupt schedules, inflate labour costs and necessitate resource reallocation, all of which can jeopardise project outcomes and overall viability.
- Unforeseen regulatory compliance issues
- Unexpected site conditions affecting worker safety
- Increased labour expenses
- Extended equipment rental periods
- Escalating overhead costs
These factors create a domino effect of financial challenges that project managers must navigate to maintain profitability and project integrity. Among the challenges they have to face are:
- Logistical problems Renewable energy sites often located in challenging environments face unique hurdles with limited accessibility, harsh weather conditions, and scarce local workforce can turn minor delays into major setbacks.
- Resource allocation challenges Dealing with downtime events, whether planned or unplanned, can consume entire technical teams, diverting resources from value-adding activities and innovation.
- Environmental damage Extended downtime in construction projects carries substantial environmental ramifications as the construction industry already accounts for approximately 40% of the UK's carbon emissions, and project delays exacerbate this issue.
Key environmental impacts include inefficient energy consumption from idle machinery, increased emissions from multiple material deliveries, and higher vehicle traffic, all affecting local air quality to prolonged on-site activities, extending the project's carbon footprint.
These factors not only intensify the project's direct environmental impact but also indirectly contribute to broader community-level emissions, underscoring the urgent need for efficient project management and innovative solutions to minimise downtime. - Regulatory compliance issues Downtime in construction projects can lead to violations of service level agreements or failure to meet regulatory requirements, resulting in financial penalties or legal actions.
And over time, frequent or prolonged downtime can damage a company's reputation, potentially eroding client trust and affecting future business opportunities.
Causes of downtime in construction projects
To maintain smooth project operations, it's crucial to identify and address the primary causes of downtime. Two significant factors stand out: rising industry costs and workforce shortages.
The construction sector has experienced price hikes, impacting both materials and equipment which, according to Wincanton, results in tradespeople losing up to 9% of their workday waiting for necessary supplies, creating a cycle of downtime and escalating costs.
Yet project deadlines are even harder to hit with a depleted workforce. Wincanton reports that nearly one-third of UK construction businesses faced worker shortages in late 2022, and this shortage is partly attributed to UK visa regulations and reliance on international labour.
How are construction companies reducing downtime?
To mitigate these risks, project managers are implementing preventative and reactive strategies through a combination of technological innovation, workforce development, and process optimisation, with several leading companies implementing innovative solutions.
To address downtime challenges on high-profile projects, Balfour Beatty, one of the UK's largest contractors, has invested in digital technologies to speed up transmission of information to managers and field engineers, improve reporting on its quality assurance processes, reduce delays in capturing field data and provide quality data for use by clients.
This approach has helped reduce unplanned downtime for projects.
Morgan Sindall has been implementing a workforce training programme which focuses on improving efficiency and reducing human error-related delays, resulting in a reduction in overall project downtime.
And Kier Group, another major player in UK construction, has adopted a proactive maintenance strategy, utilising predictive analytics to anticipate equipment failures before they occur which has reportedly decreased equipment-related downtime across its infrastructure projects.
By implementing these strategies, companies are not only improving project delivery times but also enhancing sustainability by reducing unnecessary resource consumption and emissions associated with prolonged construction periods.
******
Make sure you check out the latest news at Construction Digital, a BizClik brand.
Featured Articles
BCG report details how industries including construction need to collaborate on AI-driven energy solutions, citing data centre design as an example
Volvo Construction Equipment’s new Braås site is the first to earn the Climate Efficient Site certification, spearheading sustainability in construction
French multinational construction firm Bouygues Construction expands US presence as subsidiary Aimco lands luxurious Miami waterfront development
project