ResponsibleSteel Reports Urgent Need for Sustainable Steel
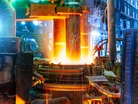
A report from ResponsibleSteel, a global, not-for-profit organisation designed to maximise steel's contribution to a sustainable world, highlights that industry-wide action is urgently needed if steelmakers are to achieve net zero.
ResponsibleSteel is driving sustainability in the steel industry. As the world's largest materials industry, steel accounts for 7-9% of global CO2 emissions, making its decarbonisation crucial for achieving net-zero goals.
ResponsibleSteel was founded in 2015 as an independent standard and certification programme, and is helping to set global benchmarks for responsibly produced net-zero steel.
These benchmarks, created collaboratively with 150 members across the steel value chain, comprise 13 ESG principles, including: corporate leadership; the responsible sourcing of input materials; labour rights; human rights; stakeholder engagement and communication; water stewardship and biodiversity.
Worldwide, ResponsibleSteel's impact is significant. There are over 80 Responsible Steel-certified sites globally, which produce an estimated 130 million tonnes of steel annually. Certified companies have an approach to sustainability that goes beyond emissions reduction, by also addressing responsible sourcing throughout the entire steel value chain.
- Certified sites increasingly source input materials from suppliers that are working to improve their environmental, social and governance performance and address ESG risks.
- Certified sites respect human rights wherever they operate, irrespective of their size or structure.
- Certified sites respect the rights of workers and support worker well-being.
ResponsibleSteel encourages steelmakers to look beyond immediate operations, to supply chain-related emissions. These so-called Scope 3 emissions are expected to account for a third of the sector's total emissions by 2050, and addressing them will be vital for a successful transition to clean energy.
But how, exactly, is ResponsibleSteel influencing and inspiring the steel industry to move closer to net zero? And how is it helping it meet its ESG challenges?.
The worldwide use of steel in the construction industry
Steel is a cornerstone of the global construction industry, accounting for over 50% of worldwide steel demand.
Its versatility, durability, and strength make it essential for everything – from skyscrapers to bridges. However, the construction industry faces significant challenges in reducing its environmental impact, with its mass use of steel and cement being among its biggest challenges.
To address this, a number of major construction companies are adopting green steel initiatives. For instance, some are exploring the use of electric arc furnaces (EAFs) and renewable energy sources to reduce emissions.
Electric arc furnaces (EAFs) use electricity to melt scrap steel, producing new steel with significantly lower carbon emissions than traditional blast furnaces.
Whereas conventional steelmaking involves reducing iron ore with coke in blast furnaces, emitting large amounts of CO2, air pollutants, and hazardous waste.
Yet green steel refers to steel produced with minimal environmental impact, often using EAFs powered by renewable electricity and recycled scrap metal as the primary raw material. This method can reduce emissions by up to 70% compared to traditional steelmaking.
As a result, construction companies are focusing on increasing the use of recycled steel, which already covers 26% of global demand.
The construction industry is responsible for about 25% of global emissions and relies heavily on steel, so addressing these ESG issues is crucial, with initiatives like low-carbon steel production and increased recycling becoming increasingly important for sustainable construction practices.
How can steel companies move closer to net zero?
ResponsibleSteel amongst many, believe that steel companies can move closer to net zero through a multi-faceted approach:
Cleaning up supply chains involves sourcing low-carbon raw materials and collaborating with suppliers to reduce emissions throughout the value chain. This approach is essential for addressing the significant portion of emissions that occur outside direct steel production.
Securing finance for carbon reduction initiatives is also crucial. Companies like ArcelorMittal, a leading steel and mining company, are leading the way by issuing green bonds to fund decarbonisation projects, demonstrating the industry's commitment to investing in sustainable practices and technologies.
Moving to green steel production is a central strategy, involving the adoption of technologies such as electric arc furnaces (EAFs), hydrogen-based reduction, and carbon capture and storage.
For instance, industrial conglomerate ThyssenKrupp, is developing hydrogen-based steel production methods, while Voestalpine, the steel and technology group, is investing in electric arc furnaces and hydrogen research.
Signing up to certification programmes like ResponsibleSteel is vital. ResponsibleSteel provides an independent standard and certification programme that sets the benchmark for responsibly produced net-zero steel.
Companies like Tata Steel, the private steel company and SSAB, the global steel company, are investing in these technologies to reduce their carbon footprint and other companies making strides includes BlueScope Steel, that is committing to net zero by 2050 and exploring low-carbon steelmaking options
In the construction sector, companies like Lendlease and Skanska are also prioritising the use of low-carbon steel in their projects and working closely with suppliers to reduce embodied carbon in their buildings.
These strategies collectively demonstrate the industry's commitment to achieving net zero, with ResponsibleSteel providing a crucial framework for progress and accountability.
ResponsibleSteel strategy to overcome barriers of adopting green steel
Green steel refers to steel produced using environmentally friendly and sustainable methods, typically involving renewable energy sources and reduced carbon emissions.
While the global green steel market is projected to grow rapidly, reaching US$624.414bn by 2032, the industry faces significant challenges in its transition.
Key barriers include high costs of renewable energy implementation, limited availability of sustainable raw materials, and uncertainties in demand, financing, and policy.
Additionally, the lack of unified standards and definitions for "green steel" complicates market development.
The ResponsibleSteel report advocates key focus areas to achieve net-zero, for: steelmakers, steel buyers, suppliers to steel makers, investors and financial institutions, policymakers, industry representatives, civil society organisations and endorsers of the steel standard principles.
Three key focus areas:
Emissions transitioning to renewable energy sources, particularly for electric arc furnaces.
Implementing innovative production techniques, such as green hydrogen technology.
Enhancing recycling efforts to increase the use of scrap steel in production, thereby reducing overall carbon footprint.
Implementing new technologies, such as electric arc furnaces and biomass reduction, alongside renewable energy sources can help also reduce emissions.
ResponsibleSteel proposes a comprehensive approach to overcome barriers in adopting green steel, centred around its International Production Standard.
This tool provides a globally consistent framework for tracking and driving the industry's transition towards sustainability.
As ResponsibleSteel CEO Annie Heaton emphasises: "The Standard enables anyone that's either buying or making steel to demonstrate they are not only driving down emissions, but also thinking responsibly about impacts on people and nature right across the value chain".
She adds: “Transforming the steel industry will require bold and universal action. No one can sit on the sidelines. Our analysis shows how certification can be used both to plan and to track the progress of every site on an equitable basis. Those who are not certified cannot be tracked.”
******
Make sure you check out the latest news at Construction Digital, a BizClik brand.
- Balfour Beatty Bolsters Digital and Procurement LeadershipProject Management
- Eco Materials Technologies Charts Sustainable ConstructionSustainability & Green Building
- Ultra-Low Carbon Cement a Green Building BoonConstruction Projects
- Construction Materials Circularity the key to SustainabilitySustainability & Green Building